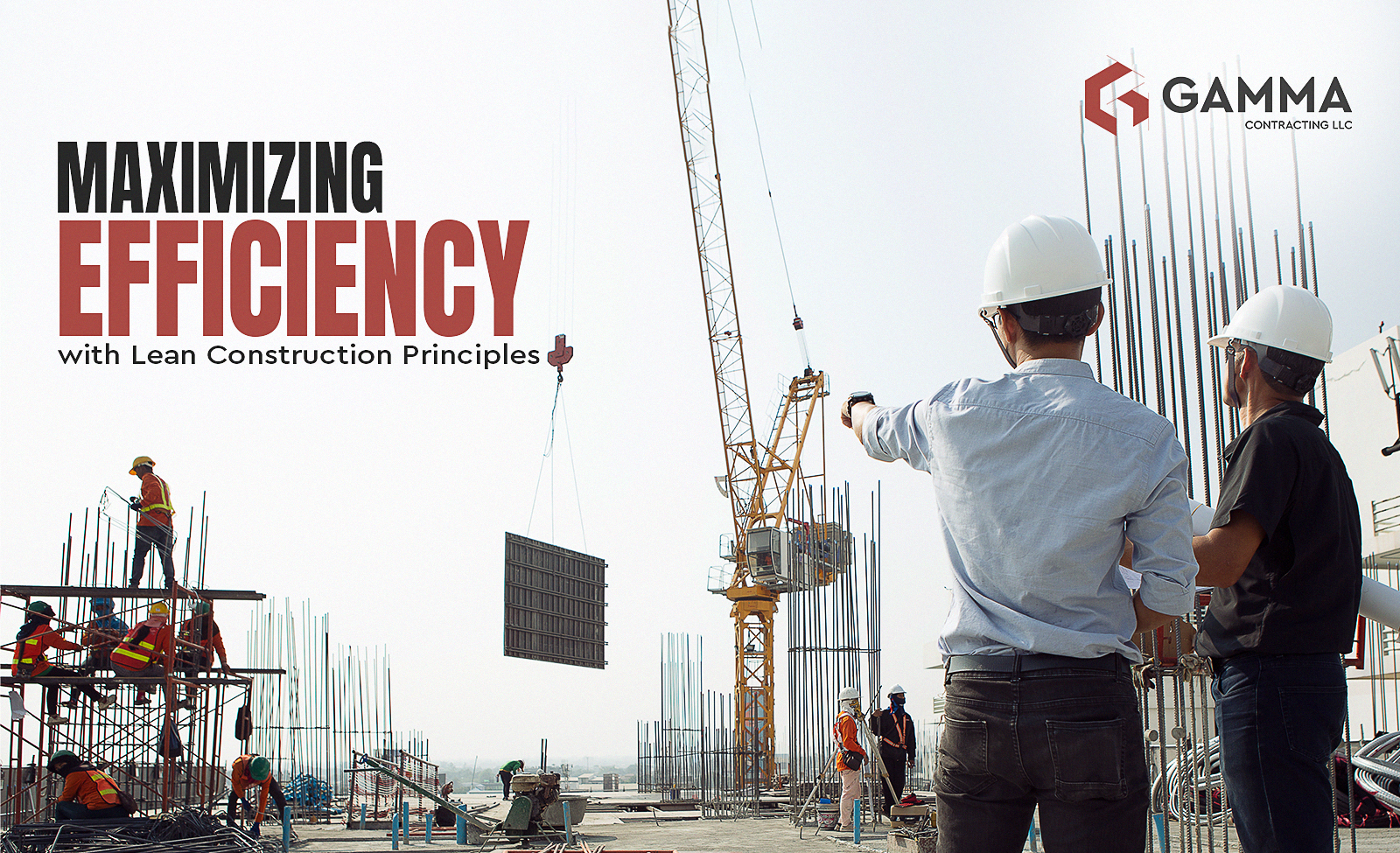
Maximizing Efficiency with Lean Construction Principles
A good construction project requires a good team of workers and expertise to create the ideal building for their customer. Construction project management is growing more complex, with short time frames and limited budgetary resources. The construction management approach selected has a significant impact on project results, such as profitability and completion time.
The Lean ideology, created by the Toyota Motor Company in the 1950s, attempts to enhance productivity using strategic thinking. Construction companies are increasingly adopting the Lean methodology, which highlights providing value for the client while also providing waste reduction in construction.
What is Lean Construction?
The Last Planner is a collection of agile development concepts that serve as the foundation for lean construction. They were created by Glenn Ballard and Greg Howell, former leaders of Toyota Training International. The goal of a lean project management approach is to maximize client value.
Lean Construction, which seeks to maximize value while eliminating waste, is inspired by Lean manufacturing concepts. It emphasizes streamlining project processes, eliminating waste, and encouraging continual development.
Lean construction can improve efficiency, reduce project durations, and boost profitability by eliminating non-value-adding operations and upholding an instantaneous delivery method for managing resources.
Lean construction uses a dynamic paradigm instead of initial designing and planning. Workers focus on finishing a particular set of duties while work is divided into brief periods. All responsibilities must be completed before the next stage, preventing work gaps. This method is also known as “pull planning.”
Lean construction is more interactive and dynamic than the waterfall process. Teams provide feedback in real-time, compared to being given an itinerary and only responding when something goes wrong.
How Does a Lean Construction Project Work?
A startling amount of time, money, and resources are being spent in the construction sector. Lean methodology increases value for everyone by streamlining logistics, fostering a mindset of cooperation, and getting rid of waste and overages.
Lean construction ensures the job is completed on schedule and at lower expenses than usual. Additionally, it aims to maximize value and reduce costs associated with project upkeep, layout, planning, and implementation.
Every project team member, including the owner, designers, and contractors, must work together to execute lean successfully. Everyone must be dedicated to identifying methods to reduce waste and boost productivity.
Lean construction uses various methods, including 5S, pull planning, just-in-time delivery, value stream mapping, and the last planner system.
Lean Construction Principles
The six lean construction concepts listed below can help businesses increase efficiency, operate projects seamlessly, cut costs, finish projects on schedule, and complete integrated projects.
Identify the Values
Customer value emphasizes the scope and implementation of a project. Therefore, it is essential that the management, designers, engineers, builders, vendors, subcontractors, workers, and all other parties involved in the construction company fully understand what value represents from the perspective of the client or the owner.
According to lean construction principles, you need to define a project’s value proposition and make sure that every person who will be engaged will have access to it. Construction firms may plan and carry out tasks more smoothly and efficiently by developing an in-depth knowledge of the values from the client’s perspective.
Define the Value Stream
The procedures necessary for providing value can be laid out if you have an explicit knowledge of the matter from the perspective of the customer. This is referred to as the value stream. It specifies what kind of labor, knowledge, tools, and supplies are required for each operation.
This encourages companies to concentrate on what matters most to customers, allowing them to set priorities and manage resources efficiently. When tools or processes are found not to add value, they may be removed, decreased, or improved to reduce the time and effort needed, improving overall value delivery.
Workflow
A construction project contains several processes, and each step must proceed continuously and without interruption for the project to be successfully completed. To have an effective workflow in building projects, the sequencing is essential. You can’t build a wall without columns. Without concrete footings, column casting is not possible.
To achieve flow, everybody involved must communicate clearly with one another. It is important to notify everyone when an element of the project is running late or ahead of plan so that suitable changes can be made to reduce waiting, action, and unnecessary inventory waste.
Waste Elimination
Lean construction prioritizes minimizing or doing away with waste whenever possible. Lean construction eliminates eight significant waste categories:
Defects: Defects are defined as everything that fails to be completed precisely the first time, leading to rework that loses time and resources.
Overproduction: This occurs in the construction industry when a project is finished ahead of plan or earlier than the subsequent activity in the procedure can be initiated.
Waiting: In the construction industry, the most prevalent situation that results in waiting occurs when personnel are prepared, but the essential supplies are still unavailable, or the necessary first task is still not finished.
Not Using Talent: Construction staff have various talents and expertise. A person’s potential, abilities, and expertise are wasted without an accurate profession.
Transport: Moving supplies, tools, or personnel to a construction site earlier than required is wasteful transportation. It may additionally refer to the unneeded transfer of material.
Inventory: Extra resources are those that are not instantly necessary. They eat up money, take up space, and degrade while not in use.
Motion: Unneeded movement, such as separating employees, equipment, and supplies, results in motion waste.
Over-processing: When elements or actions are implemented that the customer doesn’t find valuable, over-processing occurs. Ironically, this usually happens when efforts are made to eliminate other waste.
Pull Planning and Scheduling
The pull approach promoted by lean methodology bases output on actual demand rather than forecasts and estimates. This production is also known as “just-in-time” production to reduce waste and stockpiles.
Work must be distributed following downstream demand to establish reliable processes. The task schedule is created through solid cooperation and communication between employees. This cooperation is essential because it enables every person’s knowledge of the project’s aims and objectives to coincide, ensuring that the operation is effectively planned and timed.
Continuous Process
The core principle of the lean construction methodology is that processes should be improved gradually and incrementally. At each project stage, workers must determine the limiting factors, explore the potential for enhancement, and pursue perfection.
Kaizen, which stands for “change for the better” and eventually seeks continuous progress, is an essential aspect of the Lean methodology. Possibilities for improvements are discovered and addressed at each stage of the construction process. It also requires everyone to contribute and depends on overall interaction and respect to deliver a project that meets the customer’s objectives.
Conclusion
The lean methodology is a progressive technique used in almost every industry to develop the best results. The lean construction methodology is a popular method used by well-established construction companies to build better and more innovative projects within a scheduled timeline. Gamma Contracting LLC is one of the leading construction companies that can transform your dreams into reality, creating the ideal building for you.
No Comments