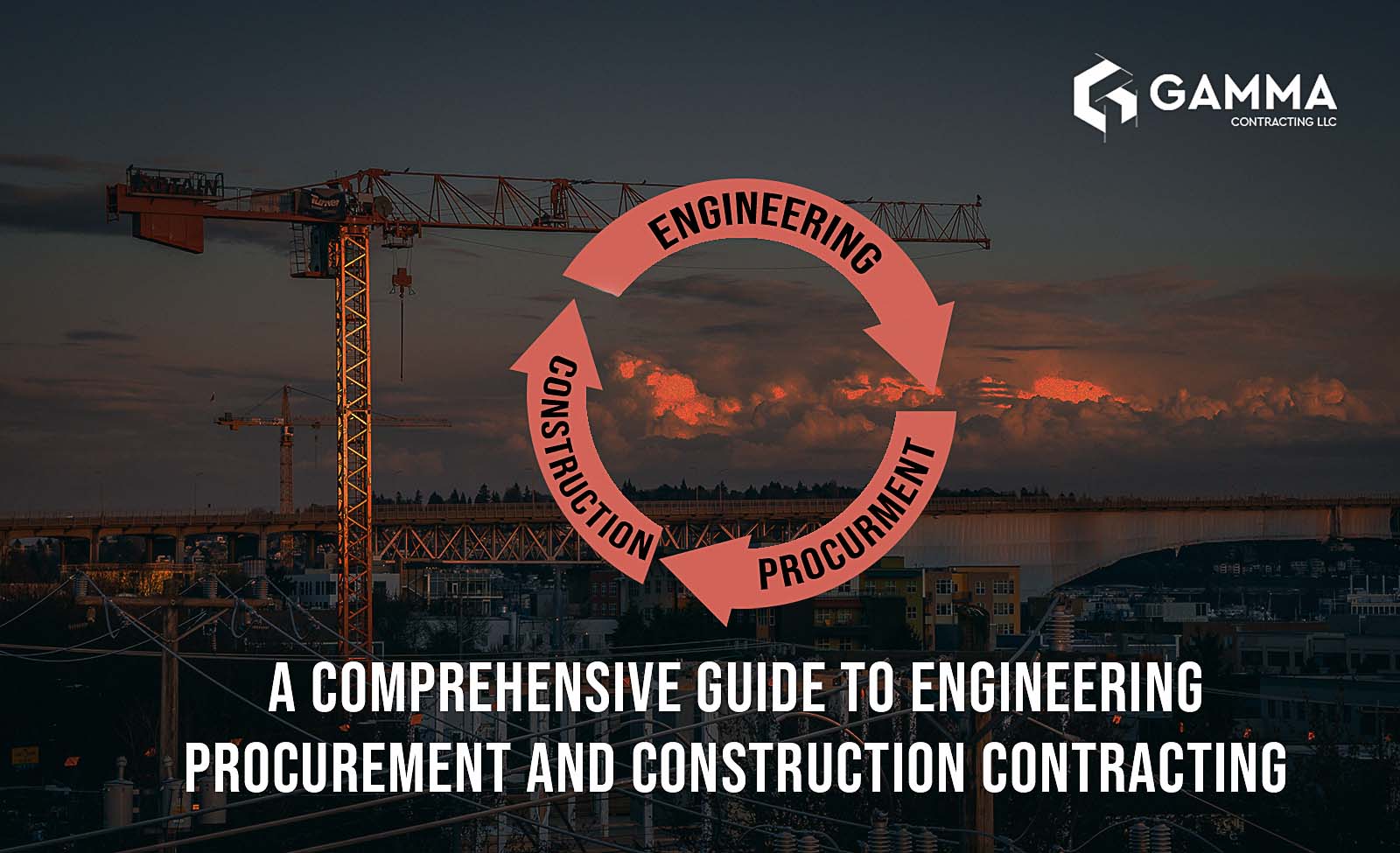
EPC Contracting: A Comprehensive Guide To Engineering Procurement And Construction Contracting
If you’ve been in and around the construction industry for some time, you’ve probably heard the term “EPC” thrown around a lot. But what exactly does it mean?
EPC stands for Engineering, Procurement and Construction, which is a type of contract commonly used in the construction industry.
EPC contracts are typically used for large-scale projects where the client wants a single point of responsibility for the entire project. This means that the contractor is responsible for the engineering, procurement, and construction phases of the project. These contracts can be complex and involve many different stakeholders, so it’s important to have a thorough understanding of how they work before entering into one.
In this blog post, we’ll cover the basics of EPC contracts, including their advantages and disadvantages, different types of EPC contracts, and what to consider when entering into an EPC contract. So if you’re curious about EPC contracts or if you’re considering entering into one, read on to learn more!
EPC Contract – An Overview
EPC Contract is a contractual arrangement that is widely used in the construction industry to minimise risks and increase efficiency in large construction projects. In an EPC Contract, a single contractor is responsible for the design, procurement, and construction of a project. This means that the contractor assumes complete responsibility for the project’s success, from start to finish. This type of contract is particularly useful for large-scale infrastructure and industrial projects, where there are many interrelated components and stakeholders
What does EPC stand for?
EPC stands for Engineering, Procurement, and Construction services. An EPC contract is a type of construction contract that involves the full cycle of a project, from design and engineering to procurement of materials and equipment to construction and installation. In other words, an EPC contract is a turnkey solution for a construction project, where the contractor takes full responsibility for the project from start to finish.
The 3 Phases of EPC!
The acronym EPC stands for Engineering, procurement, and construction which represents the three phases of this contract.
Engineering Phase: It involves designing the project and identifying the resources required. This includes conceptual design, detailed engineering, and project planning.
Procurement Phase: This phase involves the selection and procurement of materials, equipment, and services required for the project. This includes vendor selection, procurement planning, and contracting.
Construction Phase: This phase is where the actual construction of the project occurs. This phase includes project management, quality control, and commissioning.
Having a tight grasp over these three phases is crucial for any contractor entering into an EPC contract.
Key contractual obligations in an EPC contract
When a contractor signs an engineering procurement and construction contract, they are committing to take on the extensive obligations and responsibilities associated with the three distinct phases of an EPC contract. These obligations include:
Engineering Phase Obligations: During the engineering phase, the contractor must develop a detailed design and engineering plan for the project, including specifications for all materials and equipment. The contractor must also ensure that the project will meet all regulatory requirements and obtain any necessary permits and approvals.
Procurement Phase Obligations: During the procurement phase, the contractor must purchase all of the materials, equipment, and supplies needed to complete the project. The contractor must also manage the logistics of getting everything to the construction site and ensure that all materials and equipment are of the required quality and meet the specifications developed during the engineering phase.
Construction Phase Obligations: During the construction phase, the contractor is responsible for building and constructing the project according to the plans and specifications developed during the engineering phase. The contractor must also manage the construction process, hire and manage subcontractors, and ensure that the project is completed on time and within budget.
The ability of a contract construction company shines through when they are able to go above and beyond to fulfil these obligations of an EPC contract.
Benefits and Risks of EPC Contract
Like every other contract out there, EPC contracts have their own advantages and disadvantages. To ensure that contractors make an informed decision before entering into an EPC contract, it is highly advisable to have a comprehensive understanding of the advantages and potential risks associated with this type of contract.
Benefits of EPC
There are several advantages to using an EPC contract for a construction project. Some of the noticeable advantages of an EPC contract include reduced risks, cost savings, and improved project coordination. By having a single contractor responsible for the entire project, there is greater accountability and coordination between the different phases of the project. This results in fewer delays, errors, and conflicts. EPC Contract can also result in cost savings, as the contractor can leverage its expertise and purchasing power to negotiate better deals with suppliers and vendors
Risks in an EPC
Although EPC contracts offer many benefits, they also come with their own set of risks and challenges.
Some common risks and challenges of an EPC contract include higher initial costs, reduced flexibility, and increased reliance on the contractor. The contractor assumes all the risks and responsibilities associated with the project, which can result in higher initial costs. EPC Contract also limits the client’s flexibility to make changes to the project, as the contract is designed to ensure that the project is delivered according to the agreed terms.
Types of EPC Contract
There are three different types of engineering procurement and construction model of contracts that are commonly used by construction companies, with each type having its own advantages and disadvantages. The 3 types of EPC contracts are:
Lump sum or fixed price EPC Contract: In this type of contract the contractor agrees to complete the project for a fixed price.
Cost + EPC Contract: This contract involves the contractor being reimbursed for actual costs incurred, plus a fee for profit.
Target price EPC Contract: This third type of contract involves the contractor agreeing to complete the project within a target cost, with incentives for meeting or exceeding the target, and penalties for failing to meet the target.
These three EPC contacts have their own advantages and disadvantages that contractors should research before making any promising contract with the clients.
Things to Consider When Entering an EPC Contract!
There are several key considerations that clients and contractors should take into account when entering into an EPC Contract. It’s important to take into account the following three key considerations:
Legal considerations include understanding the legal requirements and drafting a detailed contract that covers all the necessary aspects of the project. This includes the scope of work, the timeline, the budget, and the quality standards.
Commercial considerations include evaluating the financial and commercial risks and opportunities associated with the project. This includes assessing the market conditions, the competition, and the financing options.
Technical considerations include assessing the technical feasibility and complexity of the project. This includes evaluating the technical requirements, the resources required, and the potential technical risks.
Conclusion
While EPC Contract is a widely used contractual arrangement in the construction industry, particularly for large-scale infrastructure and industrial projects. It has various advantages and disadvantages contractors and clients should take into consideration before entering into one.
It should be noted that EPC Contract is an effective way to minimise risks and increase efficiency in construction projects, and it will continue to be an important part of the industry for years to come.
At Gamma Contracting, we have extensive experience in EPC contracting and have successfully completed a range of projects for clients in Dubai and the UAE. Our team of experts has the knowledge and expertise to design, build, and install complex projects, and take pride in delivering high-quality solutions to our clients as one of the top engineering procurement and construction companies in UAE.
Also read: TIPS AND TRICKS FOR OVERCOMING CHALLENGES IN CONSTRUCTION PROJECTS.
No Comments